- WEBAPP
- DESKTOP
- TABLET
- MOBILE
- UI/UX DESIGN
- Angular JS
- Wildfly 10
- Java 8
- TEAM SCRUM
- AGILE
Designing the next-generation platform for automotive quality assurance
We helped Atlas Copco develop the new QA Platform 4.0: the latest generation of products for quality assurance in industrial production lines.
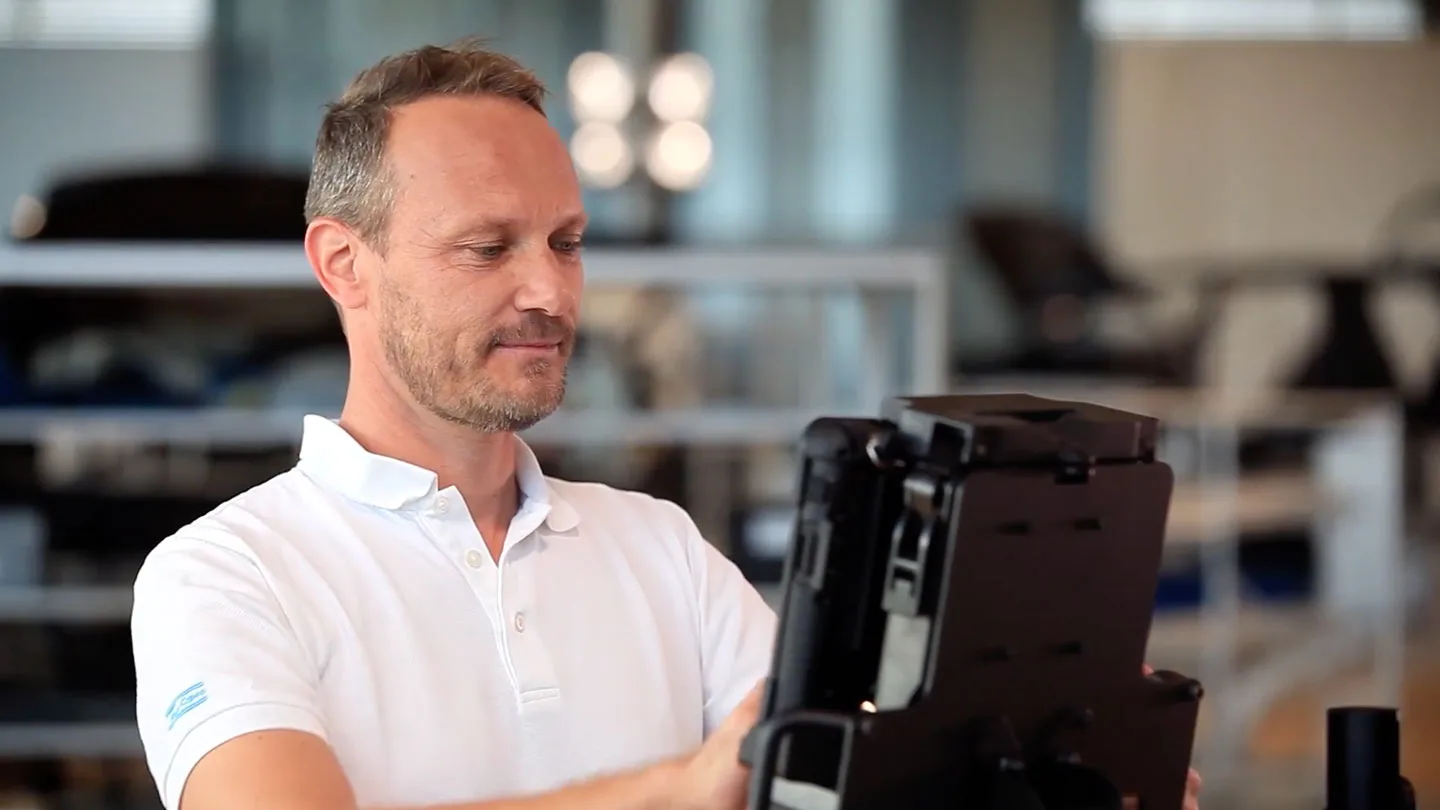
Who is Atlas Copco
Atlas Copco is a global leader in providing solutions for sustainable productivity, offering products and services focused on energy efficiency, safety, and ergonomics.
Founded in 1873, Atlas Copco has over a century of experience in innovation for sustainable productivity and operates in more than 180 countries, with operational facilities in over 90 countries. Its manufacturing is primarily based in Belgium, Sweden, Germany, the United States, India, and China.
Today, after 145 years of history, innovation, close collaboration with customers, and social commitment, Atlas Copco has become the global benchmark in the production of compressors, equipment, rock drills, and many other product areas.
The platform
This innovative platform consists of four main cores: QA Supervisor, the software for managing the entire quality assurance process; Stpad, the tablet dedicated to production line operators; STwrench, the torque wrench for measurement; and STbench, the modular and portable testing bench that can be moved along the entire production line. The designers from Thanks and developers collaborated with Atlas Copco’s teams in the development of the QA Supervisor and STpad software.
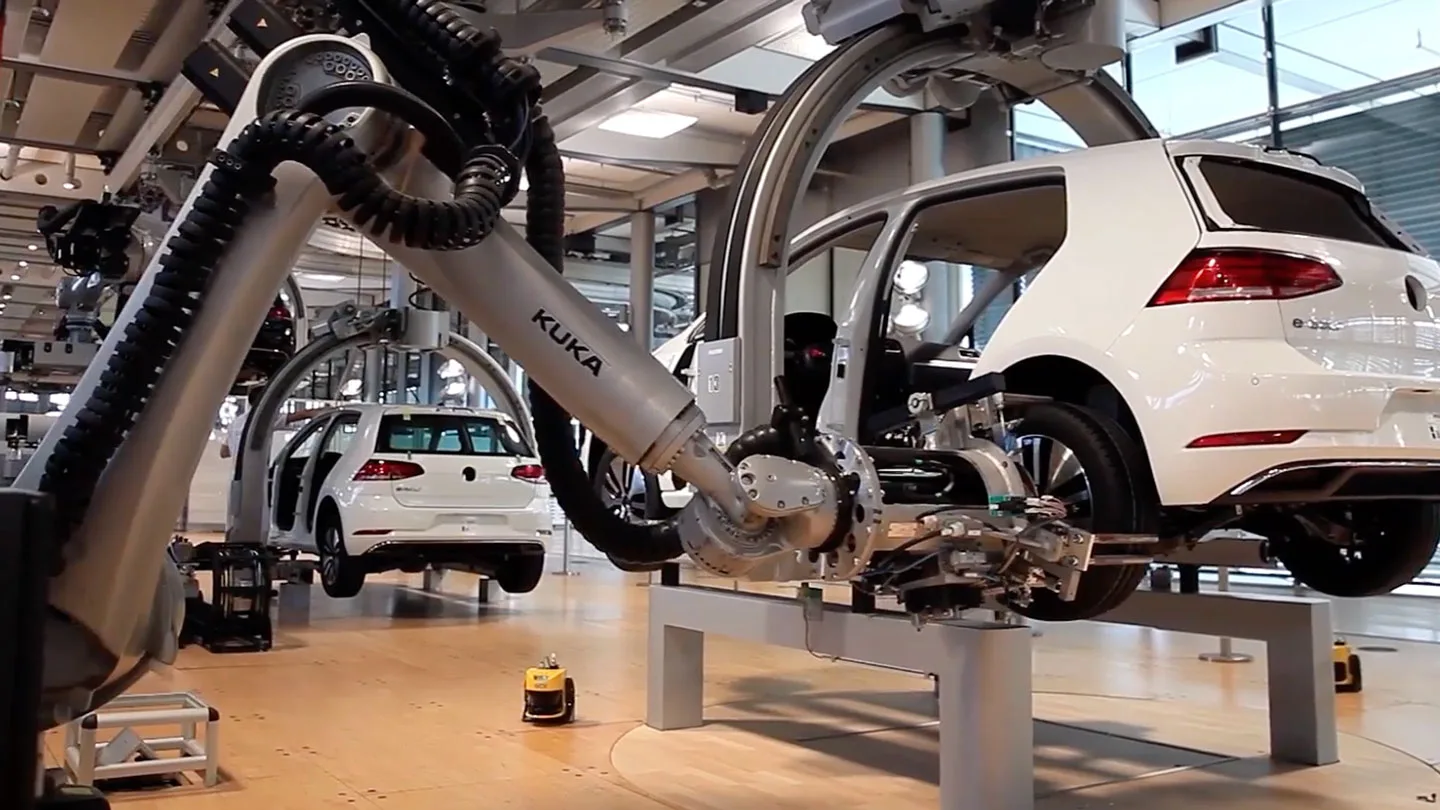
QA Supervisor
QA Supervisor is the web-based software that enables quality managers to fully monitor the activities of production line operators, the tests performed, and the measurement tools used. The quality manager has access to both a tree and topographic view of the entire area under their responsibility, through which they can obtain a real-time, comprehensive overview: from the overall production line to the details of a single joint. A notification system, focused on prevention, keeps the quality manager constantly updated, alerting them in advance about maintenance activities or potential future issues. Through the new dashboard, the quality manager can design widgets and charts according to their needs, with the goal of obtaining data and statistics to support their future strategic decisions.
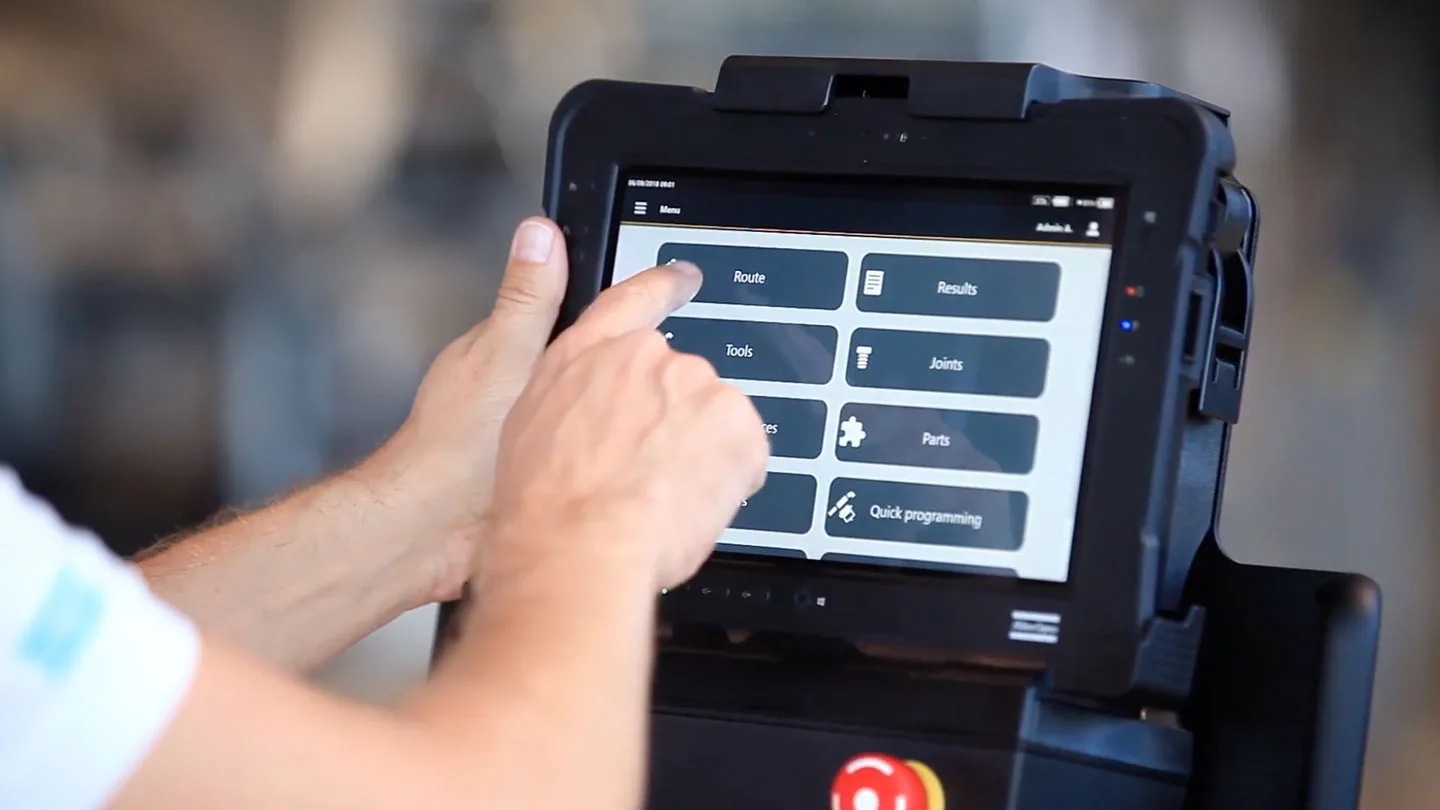
STpad
Through STpad, the operator can view their daily activity route each day. For each task, the operator is guided, step by step, through the process via STpad, with precise instructions supported by photographs and diagrams. The device also assists the operator during visual inspections/visual tests, which are further facilitated by the ability to attach photos taken on the spot.
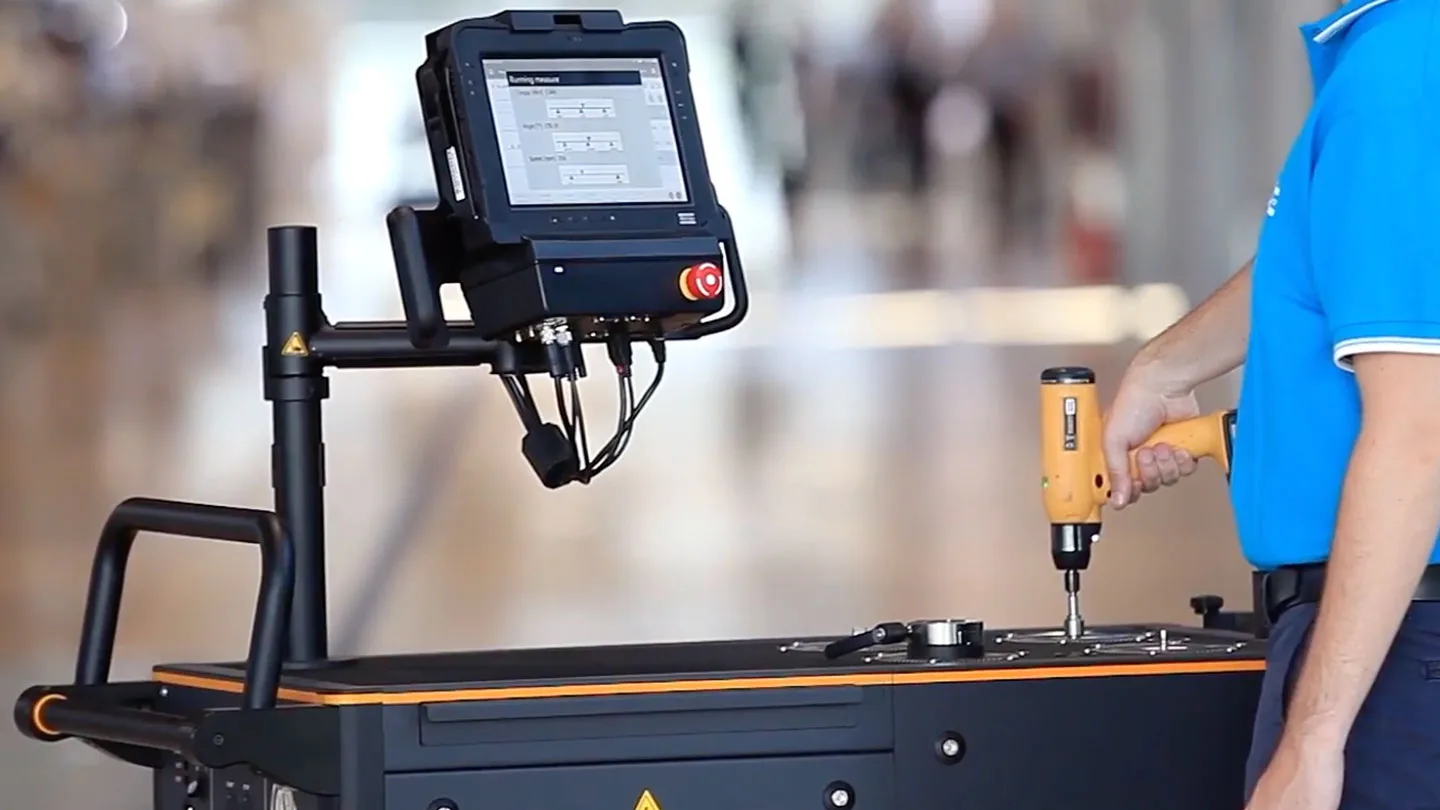
The project
Our developers and Thanks’ designers collaborated with the Atlas Copco teams in the creation of the QA Supervisor and STpad software. Both projects were organized using Scrum teams.
The designers worked closely with the Swedish design team, starting with user research and defining customer journeys, all the way to creating the information architecture and wireframes for the new product. Once the wireframes were validated, the UI design work progressed incrementally, in parallel with the development process.
For QA Supervisor, the designers were also involved in creating the HTML components to facilitate the work of the entire team.
On the development side, there was continuous collaboration between Intré’s developers and the Atlas Copco team: both teams shared a single backlog and worked on the same codebase, dividing tasks in agreement with the Product Owner to maximize development efficiency. Frequent communication, starting with shared daily scrums and periodic code reviews, enabled us to effectively integrate into the processes outlined by the Automotive SPICE standard and coordinate with Atlas Copco’s developers and testers.
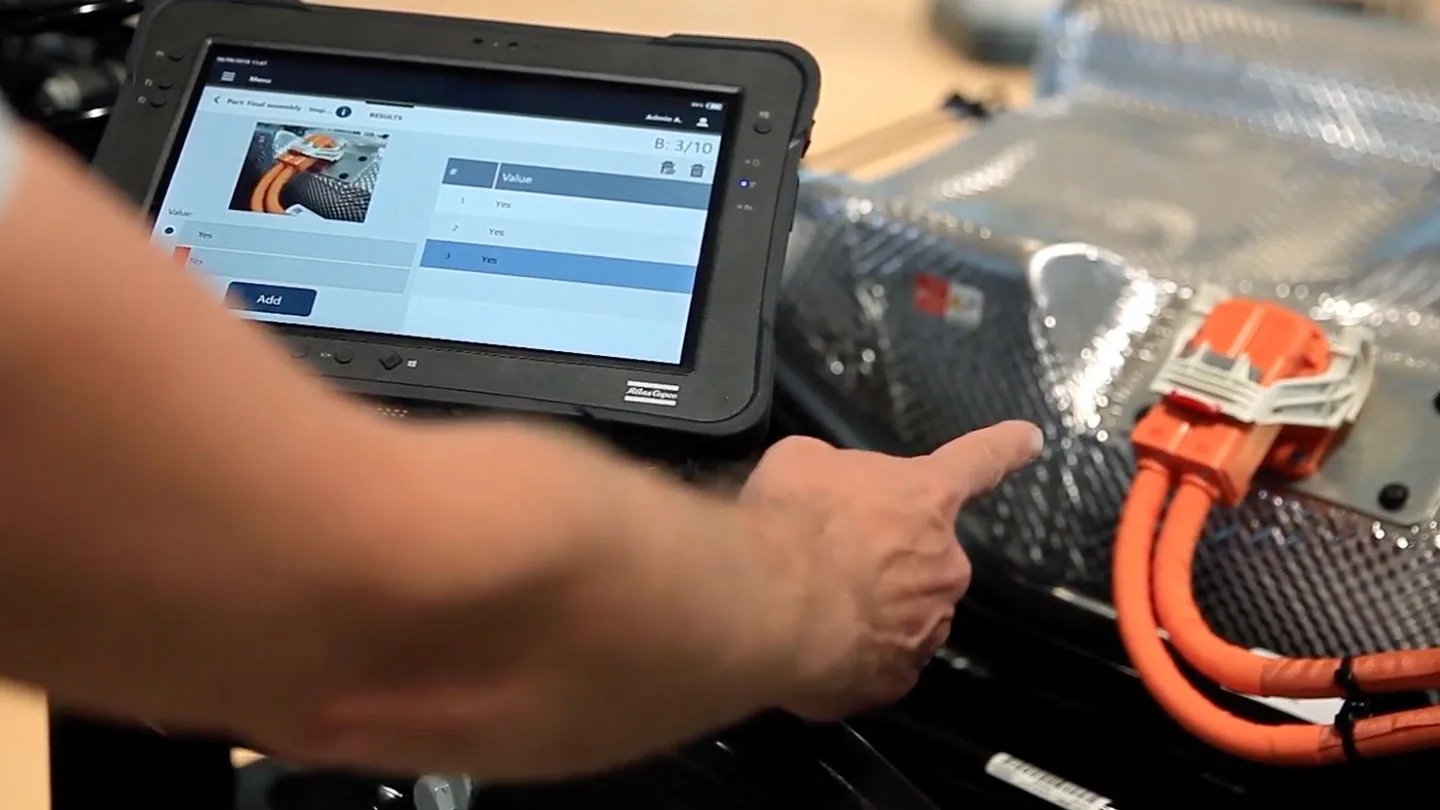
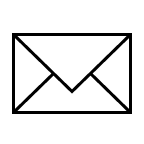